The new EPI-Vision is a remote monitoring and verification system which provides real time visibility of key Food and Occupant Safety Environmental Performance Indicators (EPI). When outside established parameters, EPI-Vision provides notifications which may directly impact Food Safety, Workers Heat Stress, and Product Quality.
Capable of serving a single location or to provide a global hub, the EPI-Vision family of systems gathers information which may include temperatures, humidity, airborne particulates, space pressurization, and wind speed. When integrated into a facility air management system, available Dynamic Control can provide significant operational savings through reduced energy and maintenance costs while providing system performance accountability . Processes with dedicated environmental control requirements such as product coolers can also be integrated into and monitored by the EPI-Vision system.
Environmental Monitoring and Verification
The new EPI-Vision System takes facility air management to the next level! Incorporating real time indoor and optional outdoor parameters, Food Safety and Indoor Air Quality are prioritized to create an intelligent system. This provides significant energy savings and reduces potential for airborne contamination by allowing for dynamic control adjustment based on actual conditions such as dewpoint, mold count, and wind speed instead of a set program assuming conditions.
Protecting Your Investments
Like any other process equipment, even the best industrial ventilation systems will fail due to improper maintenance and controls operation. The need for system performance verification is why monitoring Environmental Performance Indicators (EPI’s) is essential in food processing facilities. EPI-Vision System is able to provide push notification when the established EPI’s are outside acceptable parameters. When connected to a facility management system, dynamic control can execute commands in effort to correct the alarm condition.
What is Dynamic Control?
Space pressure differential is essential to prevent infiltration of airborne particulates through unfiltered openings such as loading docks, entry doors, and other common leakage points in the facility envelope. It is standard to have a fixed static pressure setpoint to manage this condition which ranges from 0.5 to 0.11, which is based on wind speeds of 10 to 15mph. Since these parameters are based on a fixed setting for the “worst case”, Air Management Technologies developed dynamic control for food processing facilities which adjusts the pressure setpoint based directly on wind speed with predetermined low and high limits.This translates into decreased “blasts of air” when entering a facility, prevents door opening/closing issues, and provides upwards of $30,000 annual fan and thermal energy savings in a typical bakery.
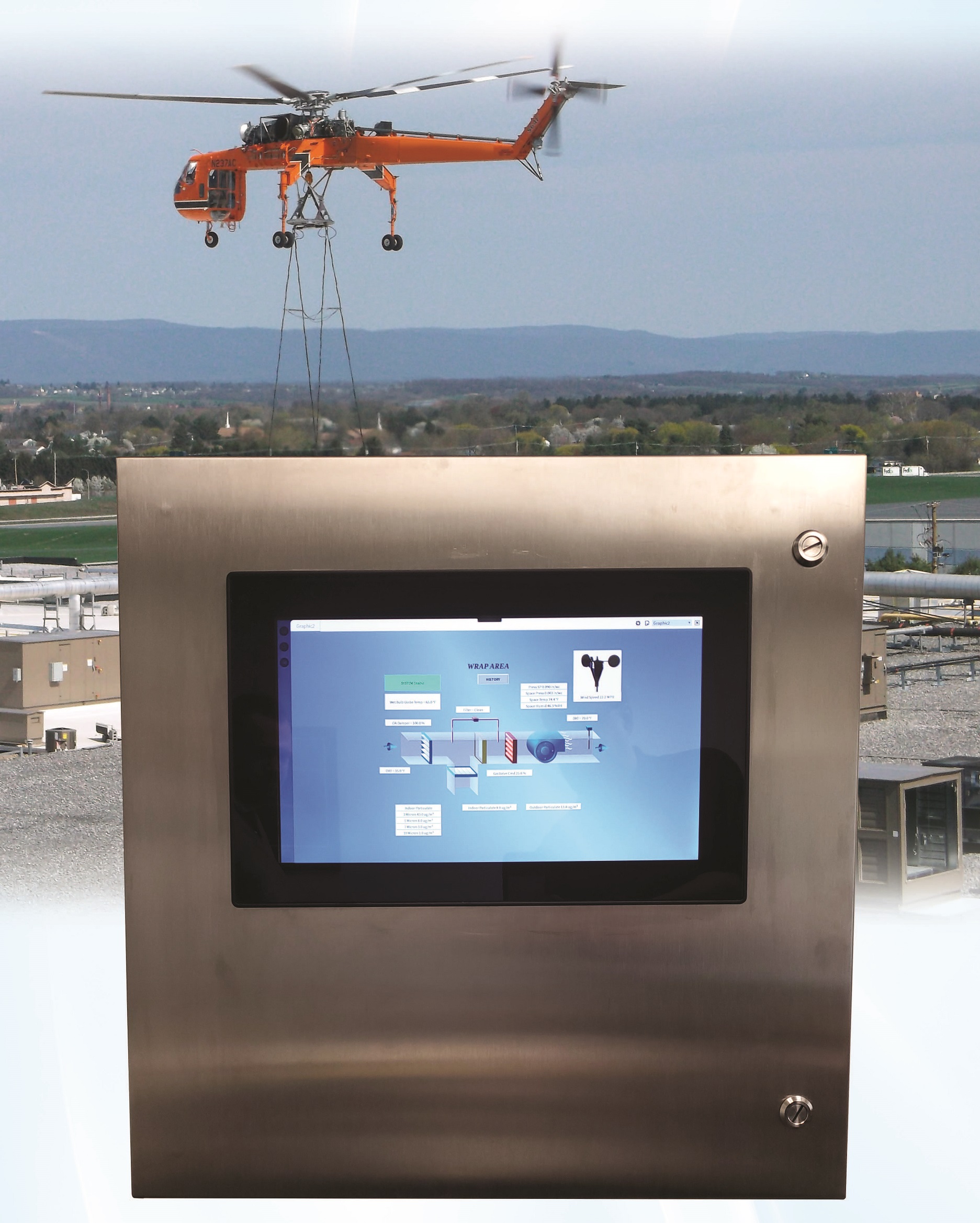
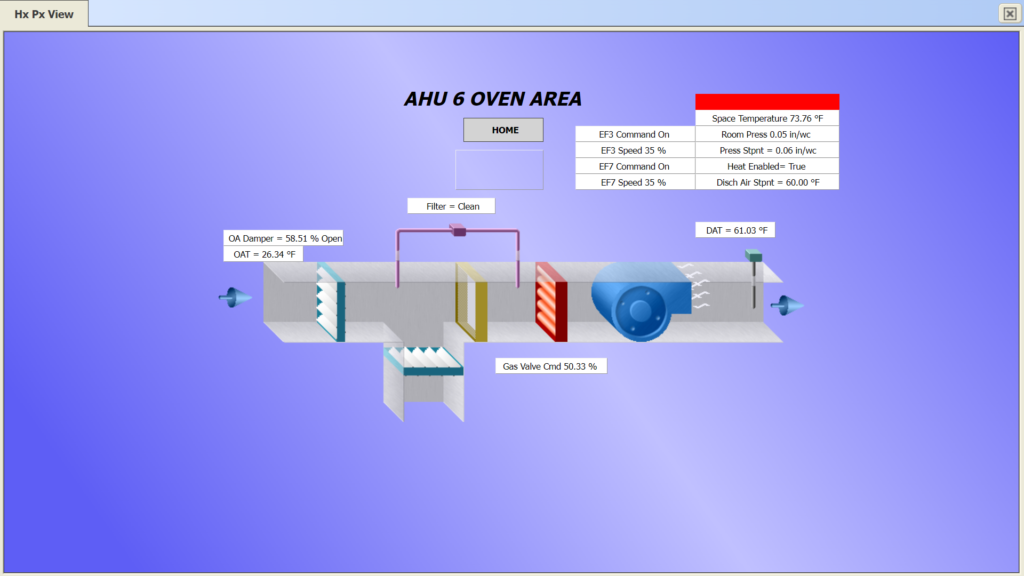
EPI-Vision
Indoor Space Temperature
Indoor Space Relative Humidity
Indoor Space Pressure
Occupant Heat Stress Measurement
EPI-Vision Pro
Indoor Space Temperature
Indoor Space Relative Humidity
Indoor Space Pressure
Indoor Particulate Sampling PM2.5 and PM10
Occupant Heat Stress Measurement
EPI-Vision Pro Elite
Indoor and Outdoor Space Temperature
Indoor and Outdoor Space Relative Humidity
Space Pressurization with Wind Speed Compensation
Indoor Particulate Sampling PM2.5 and PM10
Occupant Heat Stress Measurement
Space Dewpoint Monitoring to Prevent Condensation
Air Filtration Effectiveness
Carbon Monoxide Detection
Dynamic Control