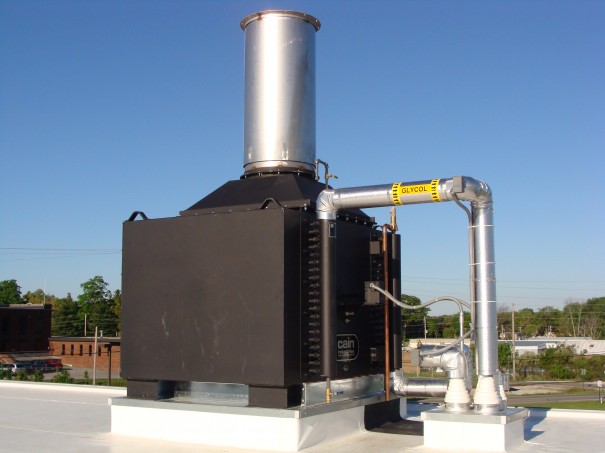
Oven / Oxidizer Waste Heat Recovery
The food processing industry is unique in that, significant potential is available by recovering the waste heat from ovens and oxidizers. This thermal waste stream may be sufficient if properly recovered, controlled, and distributed to provide enough energy to support the facility’s other thermal requirements – eliminating the need for steam boilers and their natural gas consumption. It is not uncommon to see Greenhouse Gas emissions reduced by a 1,000-tons or more per year. Energy savings will vary depending on various factors; however, in many cases, this can exceed $200,000 in high speed facilities with have both bread and bun lines. Maintenance costs are also dramatically reduced compared to steam boiler systems along with no boiler chemical requirements. In very large facilities with multiple oxidizers, the waste heat source can also be used to generate low temperature mixer refrigeration.
Closed Loop Energy Systems
Closed Loop Energy Systems (CLES) are typically defined as capturing thermal energy “waste” from a production process and returning it to offset required input energy for a different process. Closed Loop systems are not limited to only ovens – substantial energy may be available from Fuel Cells, Cookers, Digesters, Central Refrigeration Systems, and other high temperature waste streams. As an added bonus, additional potential often exists with water-treatment based thermal streams to increase grey water recycling, thus lowering facility water consumption. Every solution is engineered in-house by Air Management Technologies for your specific processes and to deliver as a Guaranteed Solution energy and environmental benefits.
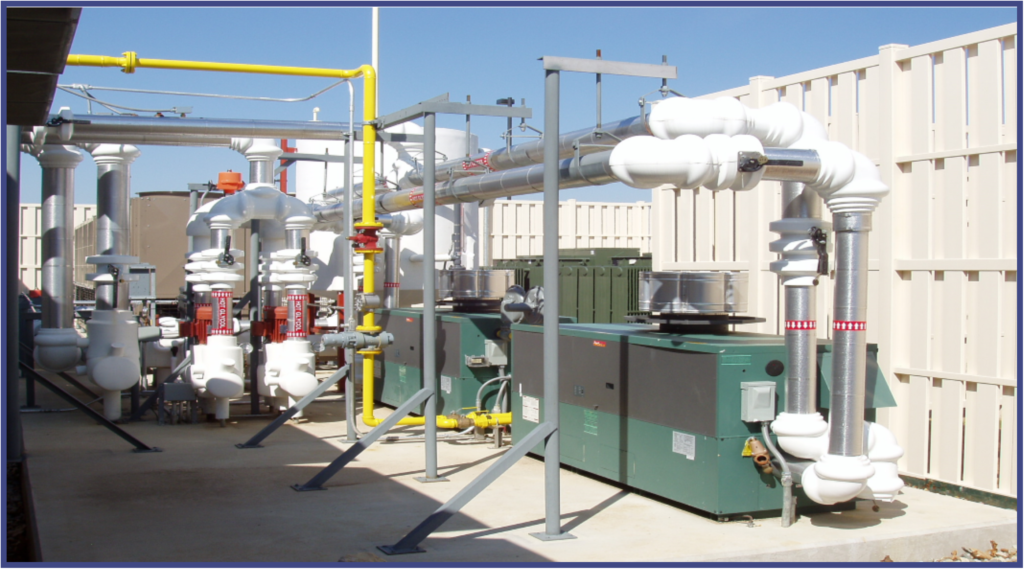
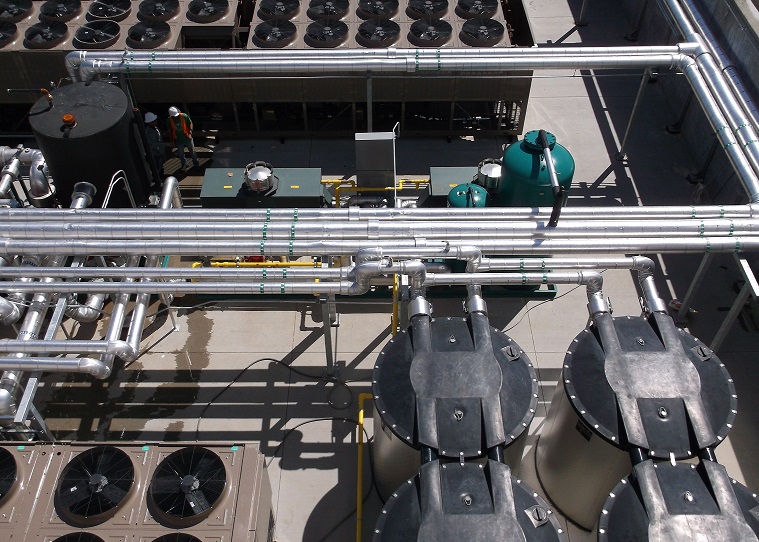
Thermal Storage Systems for Energy, Capacity, and Demand Peaking Reduction
Thermal storage is used frequently in the refrigeration industry to reduce daily / annual peak demand requirements. By utilizing storage during periods of high demand, mechanical equipment capacity is reduced saving capital expense, line voltage requirements, peak electrical demand charges, and increases the efficiency of equipment which during off-peak times is operating under partial loads. Thermal storage can save over $500,000 compared to additional mechanical infrastructure, tens of thousands of dollars in demand charges, and depending on a facility’s rate structure reduce significantly operational costs. For food processors utilizing renewable energy sources, the reduced capacity requirements may help balance onsite generation to achieve zero external energy input objectives. Incentives may also be available depending on region.
We will be glad to help you determine if thermal energy storage is an economical and environmental solution for your next project.